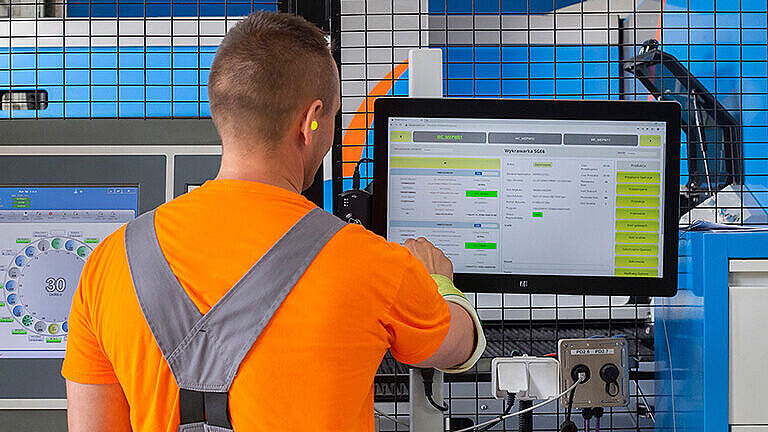
Case Study Dokładne prognozy realizacji produkcji w firmie KAN
Prognozowanie terminów dostaw gotowych wyrobów dzięki harmonogramowaniu i raportowaniu zleceń produkcyjnych.
Grupa KAN jest uznanym w Polsce i Europie dostawcą nowoczesnych systemów instalacyjnych KAN-therm. Firma zatrudnia ponad 1200 osób, posiada sieć oddziałów w Polsce i placówki w Niemczech, Rosji, Ukrainie, na Białorusi oraz na Węgrzech. Produkty KAN-therm eksportowane są do 68 krajów na całym świecie.
W zakładach produkcyjnych KAN wytwarzane są wysokiej jakości rury z polietylenu i polipropylenu, złączki z tworzyw sztucznych PPSU i PP-R oraz z mosiądzu, metalowe rozdzielacze i armatura, izolacje termiczne do ogrzewań podłogowych, a także szeroka gama wyrobów z blachy, w tym szafek instalacyjnych. W wysoko zautomatyzowanych procesach, pod nadzorem systemu zarządzania jakością ISO 9001, wykorzystuje się nowoczesne technologie, które minimalizują zużycie energii i są przyjazne dla środowiska.
Wyzwania
W związku z rozwojem firmy, konieczne stało się usprawnienie procesów biznesowych. Planowanie produkcji za pomocą arkuszy kalkulacyjnych Excel prowadziło do wielu problemów, takich jak brak dostępu do danych w czasie rzeczywistym, błędy w harmonogramach, opóźnienia w realizacji zamówień oraz trudności w zarządzaniu magazynem. W związku z rosnącym wolumenem zamówień i zwiększoną liczbą klientów firma potrzebowała nowoczesnego rozwiązania informatycznego, które umożliwiłoby efektywne planowanie, monitorowanie i kontrolowanie produkcji.
Cele
Celem wdrożenia nowego systemu było:
- Prognozowanie terminów dostaw gotowych wyrobów dla klientów, bazując na harmonogramie produkcji i raportowaniu stanu realizowanych zleceń.
- Optymalizacja dostaw surowców i prefabrykatów z magazynów, zgodnie z rzeczywistymi potrzebami wynikającymi z planu produkcji.
- Zwiększenie wydajności produkcji i zmniejszenie odchyleń technologicznych w procesie produkcyjnym.
Rozwiązanie
Po analizie dostępnych na rynku rozwiązań, Grupa KAN zdecydowała się na implementację platformy PSIasm, dostarczanej przez PSI Polska. System ten zapewnia obsługę trzech kluczowych obszarów zarządzania produkcją:
- APS (Advanced Planning and Scheduling) – zaawansowane harmonogramowanie produkcji.
- MES (Manufacturing Execution System) – monitorowanie realizacji zleceń produkcyjnych.
- SCADA – kontrola procesu produkcyjnego.
Wdrożenie systemu zostało podzielone na dwie fazy. Pierwsza, zakończona w marcu 2022 roku, obejmowała implementację modułów APS i MES w wersji standardowej, z minimalnymi dostosowaniami do specyfiki procesów produkcyjnych firmy. Na tym etapie system został zintegrowany z systemem ERP (iScala) za pomocą PSIbus – szyny integracyjnej ESB. Druga faza, planowana na połowę 2025 roku, obejmuje wdrożenie modułu SCADA.
Dzięki zastosowaniu etapowego wdrożenia zminimalizowano koszty początkowe. Dodatkowo pozwoliło to firmie na bieżąco dostosowywać funkcjonalności systemu do swoich zmieniających się potrzeb.
Efekty
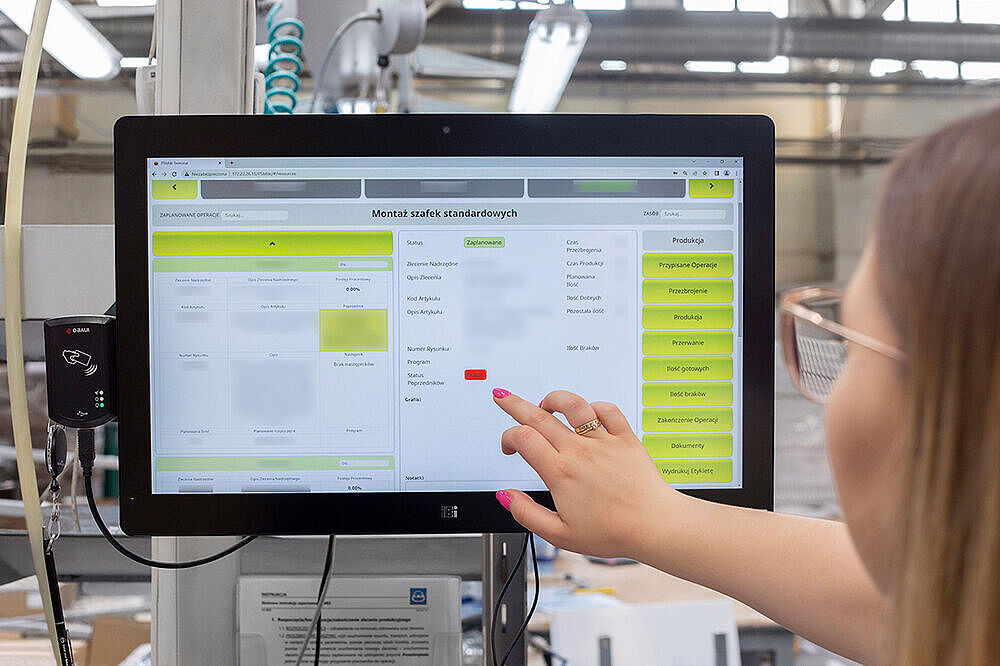
- Zautomatyzowane planowanie i harmonogramowanie umożliwiło sprawniejsze zarządzanie produkcją.
- Precyzyjne prognozowanie terminów dostaw gotowych wyrobów.
- Elastyczne i szybkie harmonogramowanie produkcji z uwzględnieniem dostępności surowców, ograniczeń technologicznych i rzeczywistej sytuację na hali produkcyjnej.
- Redukcja przestojów i błędów dzięki szybkiej identyfikacji problemów i nieplanowanych przestojów, opóźnień.
Optymalizacja dostępnych zasobów
Największą korzyścią z wdrożenia aplikacji PSI jest obiektywna informacja otrzymywana w czasie rzeczywistym – co szybko przyniosło zauważalne zmiany w obszarze obsługi klienta. To doskonałe narzędzie do optymalizacji procesów planowania i wytworzenia, którego możliwości w dużej mierze określa sam odbiorca, mając doskonałe, merytoryczne i szybkie wsparcie Zespołu PSI.
Podsumowanie
Wdrożenie PSIam zmieniło sposób zarządzania produkcją przenosząc KAN z tradycyjnego modelu opartego na papierowej dokumentacji do cyfrowego modelu Przemysłu 4.0 opartego na integracji danych ze wszystkich obszarów produkcyjnych w czasie rzeczywistym.